Elon Musk is building a spaceship that's so ambitious, some experts call it 'science fiction.' Here's what SpaceX and its engineers are up against.
- Elon Musk plans to blast a tourist around the moon in a ship made by his rocket company, SpaceX.
- The private lunar mission is meant to demonstrate a new two-part launch system called Big Falcon Rocket, which is designed to eventually bring humans to Mars.
- Engineers are said to be building a prototype of the BFR's spaceship primarily out of carbon-fiber composites.
- Exactly how SpaceX is building that spaceship isn't publicly known, but industry experts have some guesses.
- Aerospace engineers, astronauts, and Musk himself have said the first missions to Mars are likely to be perilous.
In December, a giant white tent appeared at the Port of Los Angeles. A routine permit suggested that SpaceX, the rocket company founded by Elon Musk, was using the roughly 20,000-square-foot, $500,000 facility as a "storage tent."
But Musk revealed the tent's true purpose a few months later. Inside, his engineers are building a colossal interplanetary spacecraft called BFR, the Big Falcon Rocket (or, as Musk has said, Big F---ing Rocket).
On Thursday, SpaceX announced it had selected the first private passenger to be launched in the BFR. That person, whose identity is set to be revealed on Monday, will fly around the moon, the company said.
The BFR project and its immediate lunar goalposts mark the incredible and plainly unorthodox beginning of an effort by SpaceX to colonize Mars. Though Musk may announce a moon-mission launch date on Monday, his larger goal, which he has described as "aspirational," is to launch an uncrewed cargo mission to the red planet in 2022, followed by human missions in 2024.
"He wants to have two planets for humans to live on. Some people call it crazy, but it kind of makes some sense," Marco Cáceres, a senior space analyst at the Teal Group, told Business Insider. "If something were to happen to our planet, we have an option."
Based on Musk's statements and peeks of hardware inside the tent, experts say it's clear that SpaceX workers are now building a full-scale prototype there.
The two-part BFR, as described by Musk before his private-lunar-voyage announcement, will consist of a 157-foot-tall spaceship sitting atop a 191-foot-tall rocket booster. Together, such a system would be 35 stories — taller than the Statue of Liberty.
When fully fueled, it'll weigh nearly 9 million pounds, lift up to 150 tons of cargo, and ferry those supplies to Mars with as many as 100 passengers.
On top of all that, the entire system will be 100% reusable.
That's something "we haven't seen, ever," Cáceres said. "This would be the first entirely reusable launch vehicle."
Musk's vision for the BFR places it among the most difficult engineering projects ever attempted by humans.
"We've gone to the moon. But this is an order of magnitude at least more ambitious than that — probably a couple," Steve Nutt, a materials scientist and aerospace engineer at the University of Southern California, told Business Insider of Musk's Martian ambitions. "It just sounds like science fiction."
Thus far, SpaceX has mostly kept secret whatever is going on under that white tent. People who work there will not reveal details of the project, nor will a few lucky outsiders who've been given a tour. The company declined multiple requests to provide interviews or on-the-record comments for this story.
So aerospace experts and the public are left asking how SpaceX can possibly build the enormous spaceship Musk has envisioned on the timelines he's put forth.
To get as close as possible to an answer, we spoke to a handful of aerospace industry experts who have ideas about how SpaceX will construct the BFR — including potential building materials, cutting-edge assembly processes, safety checks, and projected costs.
But they also have big questions, perhaps the most important of which is: Is society prepared to accept the high probability that some of SpaceX's missions to Mars will end in tragedy?
2019: Year of the first Mars spaceship?
Musk has said the BFR system will eventually replace every rocket and spaceship that SpaceX uses today, since it should be inexpensive to launch; that is, relative to the single-use rockets that dominate the industry.
To that end, the company recently raised hundreds of millions of dollars, much of which may go toward the BFR project. The newly announced moon voyage will also go toward the spacecraft's development, and more and more of SpaceX's 6,000 employees are also getting pulled into the effort.
Engineers started with "by far the hardest" part of the system to get right, as Musk has described it: the 16-story spaceship. The first prototype should be completed in 2019, according to Musk.
Assuming construction began with the tent's completion around December — tools for making pieces of the fuselage, or body of the spaceship, rolled through the tent's flaps months ago — this would mean a build time of about 18-24 months. By comparison, NASA's space shuttle orbiters (which are smaller than a BFR spaceship) each took about five years to make.
"It's typical SpaceX and Elon Musk stuff," Nutt said. "You don't sit around. There's a lot of pressure to do things quickly."
Once built, the spaceship prototype will most likely ride on a barge through the Panama Canal, get dropped off in Texas, and be transported inland by truck to the company's rocket facility in southern Texas. There it would start a series of short "hop" tests by late 2019, Gwynne Shotwell, the company's president and COO, indicated during a conference earlier in September.
Around the same time, workers may finish constructing SpaceX's permanent BFR factory in the Port of Los Angeles. That facility will be about 200,000 square feet, 10 times as large as the white tent.
According to SpaceX's plans, when all the parts are ready, the booster will heave the spaceship dozens of miles above Earth, detach, then land itself for inspection and refueling. Meanwhile, the spaceship will fire its engines to accelerate into orbit around Earth. (Shotwell said this may happen as soon as 2020.)
The ship will be nearly out of fuel by that point though, so SpaceX plans to launch nearly identical tanker spaceships to meet up with the first one in orbit. A series of rendezvous at about 17,500 mph would refill the spaceship's tanks with liquid methane fuel and the liquid oxygen required to burn it, though this may take about a dozen tanker flights.
"That allows us to effectively reset the rocket equation," Paul Wooster, SpaceX's principal Mars-development engineer, said during a presentation to the Mars Society in August. "We go from getting 100 tons or more into low-Earth orbit, then refill, and we can take that payload pretty much anywhere — including the surface of Mars."
The BFR's spaceship is also designed to be refilled with fuel on Mars to power its return to Earth. SpaceX plans to manufacture oxygen and methane fuel using water from Martian soil, carbon dioxide in the planet's thin air, and electricity from solar panels.
A carbon-fiber emissary from Earth
To be able to launch, refuel in orbit, endure months of flying through space, land on Mars, leave that planet, and safely return to Earth — then do all that over again — the BFR can't be an ordinary spacecraft.
That's why Musk is planning to build the entire spaceship "primarily of an advanced carbon fiber," he said in 2016.
Carbon-fiber composites are made out of many borderline-microscopic yet super-strong threads of carbon. The filaments, which are often woven together into a fabric, are then set in sticky, glue-like epoxy. When cured by heat, the epoxy hardens into an ultra-tough resin around the fibers.
In this case, the whole is greater than the sum of its parts. Many carbon-fiber composites can match or exceed the properties of steel using one-fifth of the material. Some variants can also meet the properties of aluminum — the aerospace industry's go-to, lightweight building material — at half that metal's mass.
But it's not easy to build huge structures from carbon fiber, and what SpaceX is constructing is unprecedented in the history of aviation and spaceflight.
The largest comparable vehicle ever made would be Boeing's 787 Dreamliner commercial jet airplane, which is about 50% composites by weight.
Of the spaceship, Cáceres said, "It will be massive — much bigger than anything we've ever seen."
Musk revealed the first clues about how SpaceX would manufacture a carbon-fiber vessel when he shared a photo on Instagram in April of a 40-foot-long metal cylinder with a seemingly tiny Tesla car next to it for scale.
"SpaceX main body tool for the BFR interplanetary spaceship," Musk said on Instagram. (He has since deleted his account.)
Nutt and others suspect that the tool is a rotating machine called a lathe or mandrel, which is used to apply carbon-fiber materials.
"It's a really, really big one," Nutt said of the mandrel. "I've never seen one close to that big."
Mandrels work something like a thread spooler. A robot moves along the length of a rotating mandrel, precisely unwinding rolls of carbon-fiber tape and wrapping them around the cylinder.
"You lay layer upon layer of the material. If you're going to make a spacecraft part, you'd probably have dozens of layers of material on top of each other," Greg Autry, the director of the Southern California Spaceflight Initiative who's a leading expert on the space industry, told Business Insider. (Autry has a nondisclosure agreement with SpaceX but offered to speak about the aerospace industry in general.)
Only Boeing has ever used a mandrel close to the size of the tool in Musk's photo.
'The complexity is daunting'
Though the exact materials and methods SpaceX is using aren't publicly known, Nutt said several big challenges loom if you're making carbon-fiber structures the size of apartment buildings.
One is that epoxy slowly cures on its own at room temperature. Each epoxy has a different cure rate, but the kind used to manufacture airplanes becomes unusable after about four weeks, according to Federal Aviation Administration regulations. That means SpaceX would get only about a month to build each major section of the spaceship.
Another challenge is that carbon-fiber composites don't really like to touch super-cooled, or cryogenic, liquids. But to remain a liquid, methane must be kept below -259 degrees Fahrenheit and oxygen below -297 degrees Fahrenheit.
The stakes of that challenge became clear in 2016, when one of SpaceX's Falcon 9 rockets exploded on a launchpad while carrying a roughly $200 million satellite. The most likely cause: the bursting of a carbon-fiber-wrapped tank filled with cryogenic liquid.
"It's subject to cracking and leaking," Musk said during a presentation after the explosion.
But Musk said last year that SpaceX had "developed a new carbon-fiber matrix that's much stronger and more capable at [cryogenic temperatures] than anything before."
To demonstrate that technological breakthrough, SpaceX built the biggest-ever carbon-fiber-composite fuel tank, which Musk's staff then tied to a barge, dragged to sea, filled with cryogenic liquid, pressurized beyond its limits, and made violently burst.
And there's yet another major challenge in building most of a spaceship out of carbon-fiber composites: If the material isn't cured correctly, hard-to-detect and potentially mission-ending flaws might get cooked into the spaceship's body.
To avoid such disastrous defects, carbon-fiber composites must get squeezed under as much pressure as possible to push out bubbles, collapse voids, and ensure strong bonds.
"That's typically done with a giant pressurized oven, like a pressure cooker, that's called an autoclave," Autry said. "But these things are very expensive."
Cáceres said an autoclave the size SpaceX might require would be a similar size to the one used for 787 airplane fabrication, and that custom-built device cost Boeing up to $300 million. So Nutt thinks SpaceX is likely to go about it a different way.
"I think they're going to cure it in an oven," Nutt said. "You can make an oven for one-half to one-tenth the cost of an autoclave."
If he's right, that means SpaceX would put each finished section into a giant, heat-resistant plastic bag, suck out enough air to smoosh the carbon-fiber layers together, and heat everything.
Workers might then disassemble the mandrel to free the cured and hardened section. When all the big pieces are done — perhaps two or three "barrel sections," as Wooster calls them, plus one pointy nosecone — SpaceX would somehow combine them all into a single fuselage.
To join the sections of Boeing's Dreamliner together, the company uses about 50,000 metal fasteners. But initially this led to major headaches, since thousands of fasteners had to be replaced on about a dozen of the earliest planes after problems appeared during pressurization tests.
Such a problem would only be worse for a spaceship. Temperature differences in space can be hundreds of degrees, and various aerospace materials expand and contract at different rates.
"There are so many different parts of this thing, the complexity is daunting," Nutt said. "There will have to be a variety of materials and joining methods to accomplish everything this has to accomplish."
Nutt said this will be all the more reason for critics to laud any triumphs by SpaceX.
"I think if he succeeds, then people should appreciate what he had to overcome — what the company had to overcome," Nutt said, adding, "I wouldn't recommend betting against Elon Musk."
How to avoid death by defect or damage
Whatever is going on under that big white tent, one thing is certain, Nutt said: SpaceX needs to very carefully check its work.
That's because carbon-fiber composite materials don't easily signal cracks, voids, or other defects.
"When a metal part gets damaged, there's usually a dent or a scratch or something like that," Nutt said. "With composite parts, there can be damage and no manifestations at the surface. It's all subsurface."
To inspect carbon-fiber sections, SpaceX may need to painstakingly cover every square inch with ultrasound scanners.
"You may have some structural problems on an aircraft, but the aircraft won't explode," Cáceres said. "But on a rocket, leaks, cracks, and instability — those things can be catastrophic. It explodes and people die."
Nutt thinks that to reduce that risk, SpaceX is likely to follow an industry standard practice of making demonstration parts, cutting out foot-long sample pieces, torturing those in stress tests, then inspecting them. Engineers could feed that test data into computer models and simulators to estimate how a full-size spaceship might fare.
"It's a fairly tedious process, and that's one reason materials in aerospace are introduced extremely slowly," Nutt said.
Eventually, SpaceX will build and test a full-scale spaceship. And there's a good chance the first one will fail spectacularly.
"When you're building something this big, the only real way to test it is once you've completed it, and you launch it," Cáceres said. "You better have a lot of money, because you're probably going to go through a lot of big, big structures before you get the one that works."
SpaceX is not under any delusions about avoiding snags. Many of its experimental launches and landings have ended in fiery explosions. The company has also weathered failures with operational rockets that resulted in the loss of expensive payloads. And earlier this year, Musk warned that SpaceX's largest-ever rocket, Falcon Heavy, could blow up during its maiden launch. (It did not.)
"Knowing Elon, I think you can expect him to experiment and do iterative testing — he always has — and it may work, or it may not," Autry said.
Once the spaceship is on a mission, however, in-flight inspections and repairs will still be essential.
"It's such a long mission," Nutt said. "I think the chances of some kind of damage or failure en route are much greater than a mission of days or weeks that we've seen in our lifetime."
Tiny pieces of rock or comet dust are extremely dangerous in space, since they can impact a spacecraft at thousands of miles per hour. One strike by a millimeter-long object could cripple a deep-space mission if it doesn't have repair capabilities.
"Those things can go right through any kind of structure and do a lot of damage," Nutt said. (The video below shows a 0.1-inch aluminum sphere striking a carbon-composite material at 15,800 mph.)
Yet carbon-fiber composites are extraordinarily tricky to fix, even on Earth. For example, Nutt said, when the Department of Defense needs to repair carbon-fiber-composite jet fighters, workers sand and sheen a damaged area, slather on layers of epoxy using "fancy trowels," put the damaged area under vacuum, and heat it. And that's what he calls the "crude" method.
"Things that you might be able to repair with some difficulty on Earth are orders of magnitude more difficult to execute and accomplish in space," Nutt said. "It's a big structure with a lot of components. The chances of failure are not zero. So you have to worry about those things and have contingency plans for all of them."
Spaceships don't grow on trees
Cáceres said each BFR launch might cost about $10 million, give or take, with most of that going toward fuel (since the system is designed to be reused many times). By comparison, the Falcon Heavy rocket costs close to $100 million per launch but can carry about half the payload of a BFR spaceship.
However, Cáceres' estimate doesn't include the capital needed to build and test the BFR in the first place.
"If I had to venture to guess, I would say it would be somewhere in the $4 billion to $5 billion range," Cáceres said of those development costs, adding that if Musk "is really unlucky and there continue to be setbacks, it could be more than that."
Delays can add enormously to the final bill, Cáceres said.
"That's why so many government space programs tend to be so expensive — because they just go on and on, forever and ever, for technical reasons as well as budgetary and political reasons," he said.
But Cáceres expects that if SpaceX shows enough progress, NASA could become interested and invest in the system's further development, helping to offset the company's costs.
"Ultimately, BFR could become a joint US government–SpaceX program," Cáceres said. "That would be my guess, eventually, because as much as I admire the success of SpaceX, this just seems like something too massive and too complicated for one company alone to handle."
If SpaceX successfully flies a tourist around the moon, that could serve as an audacious advertisement to NASA and lawmakers who control the government's purse strings: "Buy me," it would tacitly say.
'Rockets are going to explode, and people are going to die'
Before BFR is built and a passenger is launched toward the moon, SpaceX must ace a more immediate task.
For the first time in its 16-year existence, the company is about to launch NASA astronauts to the International Space Station.
"If BFR is going to work, then using Falcon 9 or Falcon Heavy rockets to launch a crewed capsule has to be successful," Cáceres said. "SpaceX has got to get into a rhythm where launching people to the space station becomes a matter of habit."
But even if those crewed flights go smoothly, the world must be prepared for an uncomfortable and inevitable moment: death on or en route to Mars.
When Musk presented his plan to reach the red planet to the International Astronautical Congress in 2016, an audience member asked who the first people to go on SpaceX's Mars mission should be.
"The first journey to Mars is going to be really very dangerous. The risk of fatality will be high; there's just no way around it," Musk said, adding, "It would be basically: Are you prepared to die? And if that's OK, then you're a candidate for going."
Cáceres, who was watching the presentation, said he was struck by Musk's honesty.
"I immediately thought: That's not something that any representative, any CEO from a company, or any NASA administrator would say," Cáceres said. "That's about as blunt as you can be, and I think he was being very truthful."
Is Earth ready for a trail of death leading to the red planet?
A significant chunk of the US population now considers sending people to the space station to be somewhat routine and fairly safe, minus two deadly space shuttle accidents, Cáceres said. But the early days of the commercial railroad, automobile, and aviation industries were very deadly.
Cáceres said we should expect a similar outcome if SpaceX is to achieve its goal of making interplanetary travel similarly commonplace.
"SpaceX is going to fail in the future — rockets are going to explode, and people are going to die," he said. "That is what everyone has to totally understand."
Chris Hadfield, a retired astronaut, has compared the dangers of using current technologies to reach Mars to an even earlier period of human history, when explorers circumnavigated Earth on perilous, yearslong ocean voyages.
"The majority of the astronauts that we send on those missions wouldn't make it," Hadfield told Business Insider of attempts to reach Mars. "They'd die."
Seasoned astronauts would be likely to attempt the trip regardless — and already the first private lunar voyager has signed up.
But Cáceres wonders how deep our enthusiasm for reaching toward the stars runs.
"If we want to actually open space to average people rather than government astronauts, then we've got to accept that there's going to be a lot of fatalities," he said. "We can either decide that that's acceptable or it's not, in which case we don't explore space any more than we have already."
Join the conversation about this story »
NOW WATCH: Elon Musk wants to live on Mars, but this planetary scientist says that's a terrible idea
Contributer : Tech Insider https://ift.tt/2MBbC8U
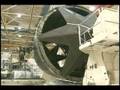
No comments:
Post a Comment